Výber povrchovej úpravy je problém, ktorému čelí každý dizajnér. K dispozícii je veľa druhov možností povrchovej úpravy a dizajnér na vysokej úrovni by mal brať do úvahy iba ekonomiku a praktickosť dizajnu, ale venovať pozornosť aj procesu montáže a dokonca aj environmentálnym požiadavkám. Nižšie je uvedený stručný úvod k niektorým bežne používaným povlakom pre upevňovacie prvky na základe vyššie uvedených princípov, pre odkaz od lekárov pripevňovania.
1. Elektrogalvanizácia
Zinok je najbežnejšie používaný náter pre komerčné upevňovacie prvky. Cena je relatívne lacná a vzhľad je dobrý. Bežné farby zahŕňajú čiernu a vojenskú zelenú. Jej protikorózne výkonnosť je však priemerná a jeho výkonnosť proti korózii je najnižšia medzi vrstvami pokovovania zinku (povlaky). Všeobecne platí, že test neutrálneho soľného spreja z galvanizovanej ocele sa vykonáva do 72 hodín a špeciálne tesniace látky sa tiež používajú, aby sa zabezpečilo, že test neutrálneho soli trvá viac ako 200 hodín. Cena je však drahá, čo je 5-8-násobok ceny obyčajnej galvanizovanej ocele.
Proces elektrogalvanizácie je náchylný k vodíkovému styku, takže skrutky nad stupeň 10.9 sa vo všeobecnosti nelieči s galvanizáciou. Aj keď sa vodík môže po pokovovaní odstrániť pomocou rúry, pasivačný film sa poškodí pri teplotách nad 60 ℃, takže odstraňovanie vodíka sa musí vykonať po elektrotechnike a pred pasiváciou. To má zlú prevádzkovú prevádzku a vysoké náklady na spracovanie. V skutočnosti všeobecné výrobné závody aktívne neodmiestajú vodík, pokiaľ nie sú nariadené konkrétnymi zákazníkmi.
Konzistencia medzi krútiacim momentom a predtiahnutím sily galvanizovaných upevňovacích prvkov je zlá a nestabilná a vo všeobecnosti sa nepoužívajú na spojenie dôležitých častí. Aby sa zlepšila konzistentnosť predpätia krútiaceho momentu, môže sa na zlepšenie a zvýšenie konzistencie predpätia krútiaceho momentu použiť aj metóda potiahnutia mazacích látok po pokovovaní.
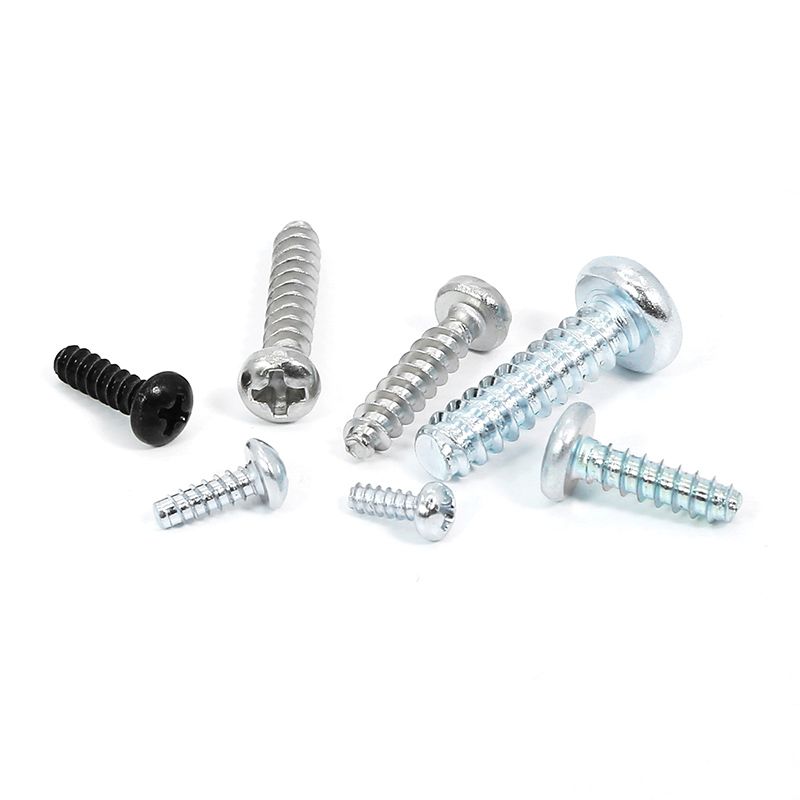
2. Fosfátovanie
Základným princípom je, že fosfát je relatívne lacnejší ako galvanizácia, ale jej odolnosť proti korózii je horšia ako galvanizácia. Po fosfátovaní by sa mal aplikovať olej a jeho odolnosť proti korózii úzko súvisí s výkonom aplikovaného oleja. Napríklad po fosfátovaní, nanášaní všeobecného proti hrdzavého oleja a vykonávaní testu neutrálneho soľného spreja iba na 10-20 hodín. Aplikácia vysoko kvalitného proti hrdzavého oleja môže trvať až 72-96 hodín. Jeho cena je však 2-3-násobok ceny všeobecnej fosfátovanej ropy.
Existujú dva bežne používané typy fosfátu pre upevňovacie prvky, fosfát na báze zinku a fosfát na báze mangánu. Fosfácia založená na zinku má lepšiu mazaciu výkonnosť ako fosfácia založená na mangáne a fosfát na báze mangánu má lepšiu odolnosť proti korózii a odolnosť proti opotrebeniu ako zinkový pokovovanie. Môže sa použiť pri teplotách v rozmedzí od 225 do 400 stupňov Fahrenheita (107-204 ℃). Najmä pre spojenie niektorých dôležitých komponentov. Ako sú skrutky s prívodom a matice motora, hlava valca, hlavné ložisko, skrutky zotrvačníka, skrutky a matice kolies atď.
Skrutky s vysokou pevnosťou používajú fosfátovanie, ktoré sa tiež môžu vyhnúť problémom s vodíkovým stĺpikom. Preto skrutky nad stupňom 10.9 v priemyselnom poli vo všeobecnosti používajú fosfátované povrchové ošetrenie.
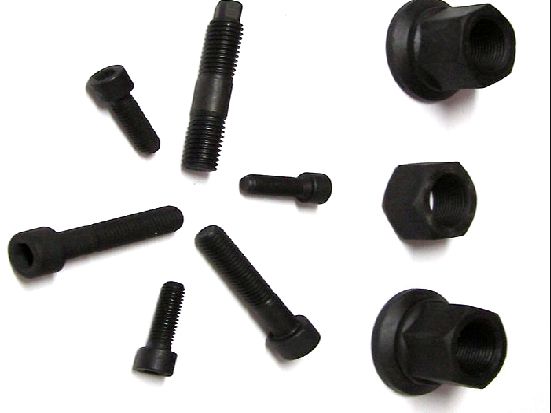
3. Oxidácia (sčernenie)
Blacking+Oiling je populárny náter pre priemyselné upevňovacie prvky, pretože je najlacnejší a pred spotrebou paliva vyzerá dobre. Vzhľadom na jej sčernenie nemá takmer žiadnu schopnosť prevencie hrdze, takže rýchlo hrdzaví bez oleja. Dokonca aj v prítomnosti oleja môže test soľného spreja trvať iba 3-5 hodín.
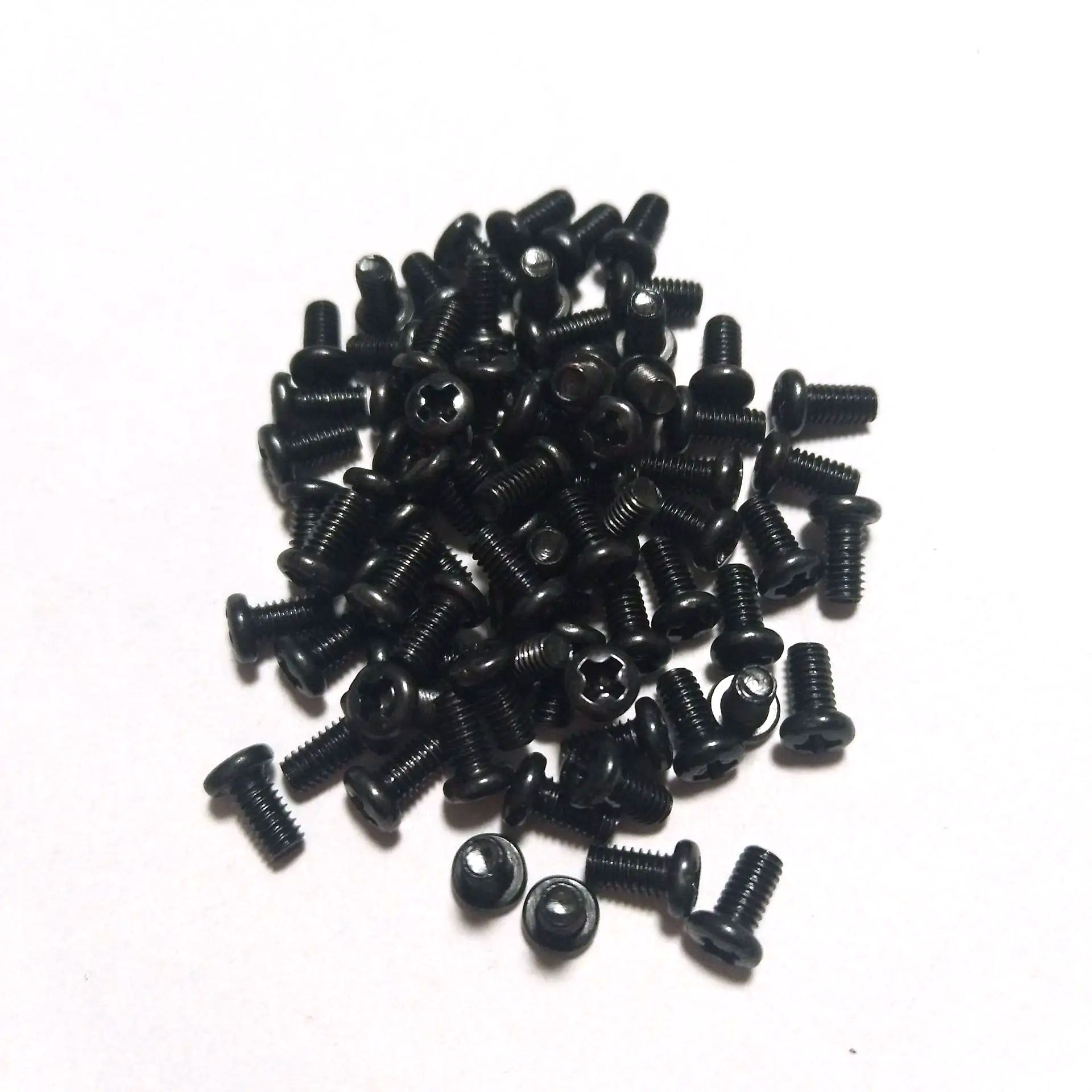
4. Elektroplatná oddiel
Kadmiové pokovovanie má vynikajúcu odolnosť proti korózii, najmä v morskom atmosférickom prostredí v porovnaní s inými povrchovými úpravami. Náklady na úpravu odpadových kvapalín v procese elektroplatovania kadmia sú vysoké a jeho cena je približne 15-20-násobok ceny elektroplatu zinku. Preto sa nepoužíva vo všeobecných odvetviach, iba pre konkrétne prostredie. Upevňovacie prvky používané pre ropné vŕtacie plošiny a lietadlá HNA.
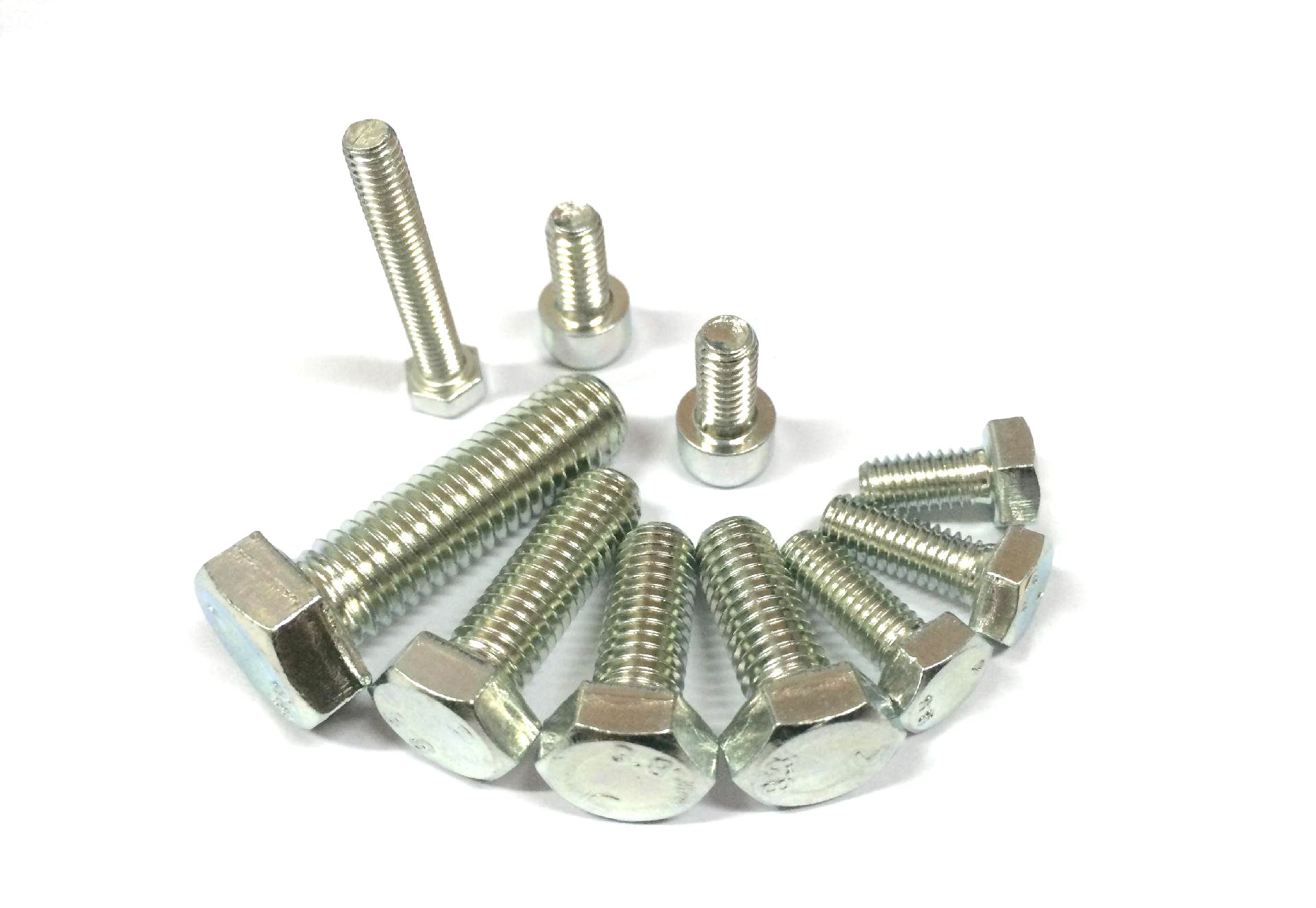
5. Chrómové pokovovanie
Povlak na chróm je v atmosfére veľmi stabilný, nie je ľahké zmeniť farbu a stratiť lesk a má vysokú tvrdosť a dobrú odolnosť proti opotrebeniu. Použitie pokovovania chrómu na upevňovacích prvkoch sa všeobecne používa na dekoratívne účely. Zriedkavo sa používa v priemyselných poliach s vysokými požiadavkami na odolnosť proti korózii, pretože dobré upevňovacie prvky s chrómom sú rovnako drahé ako nehrdzavejúca oceľ. Iba vtedy, keď je pevnosť z nehrdzavejúcej ocele nedostatočná, namiesto toho sa používajú chrómované upevňovacie prvky.
Aby sa zabránilo korózii, meď a nikel by sa mali najskôr poklepať pred chrómovým pokovovaním. Chrómový povlak vydrží vysoké teploty 1200 stupňov Fahrenheita (650 °). Existuje však aj problém s vodíkovým stykom, podobný elektrogalvanizovaniu.
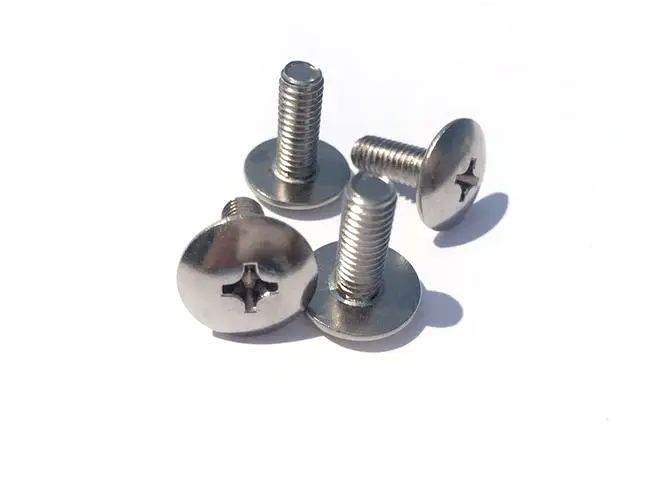
6.
Používa sa hlavne v oblastiach, ktoré vyžadujú proti korózii aj dobrú vodivosť. Napríklad odchádzajúce terminály batérií vozidla.
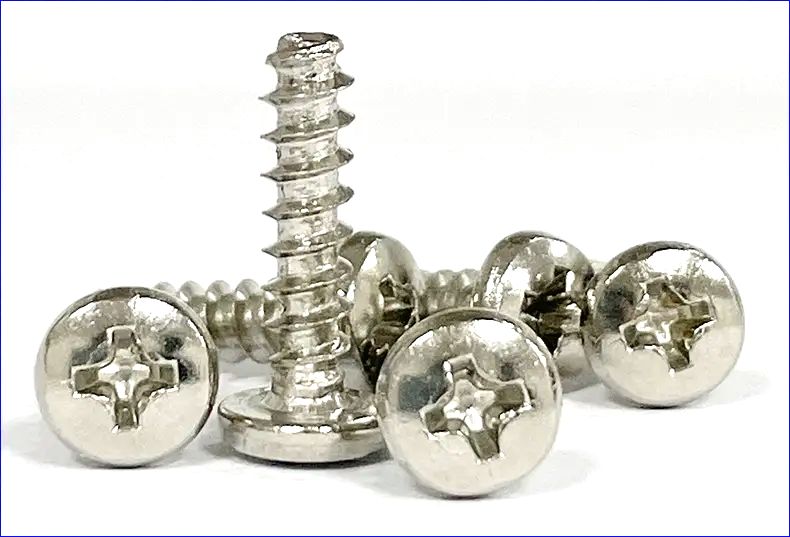
7. Horúcne galvanizovanie
Galvanizácia horúcich ponorov je tepelný difúzny povlak zinku zahrievaný na tekutinu. Hrúbka povlaku je medzi 15 a 100 μm. A nie je ľahké ovládať, ale má dobrý odolnosť proti korózii a často sa používa v inžinierstve. Počas procesu galvanizácie horúcich ponorov dochádza k vážnemu znečisteniu vrátane odpadu zinku a pary zinku.
V dôsledku hrubého povlaku spôsobil ťažkosti s skrutkovaním vo vnútorných a vonkajších závitoch v upevňovacích prvkoch. Vzhľadom na teplotu spracovania galvanizácie horúcich hornín sa nemôže použiť pre upevňovacie prvky nad stupeň 10.9 (340 ~ 500 ℃).
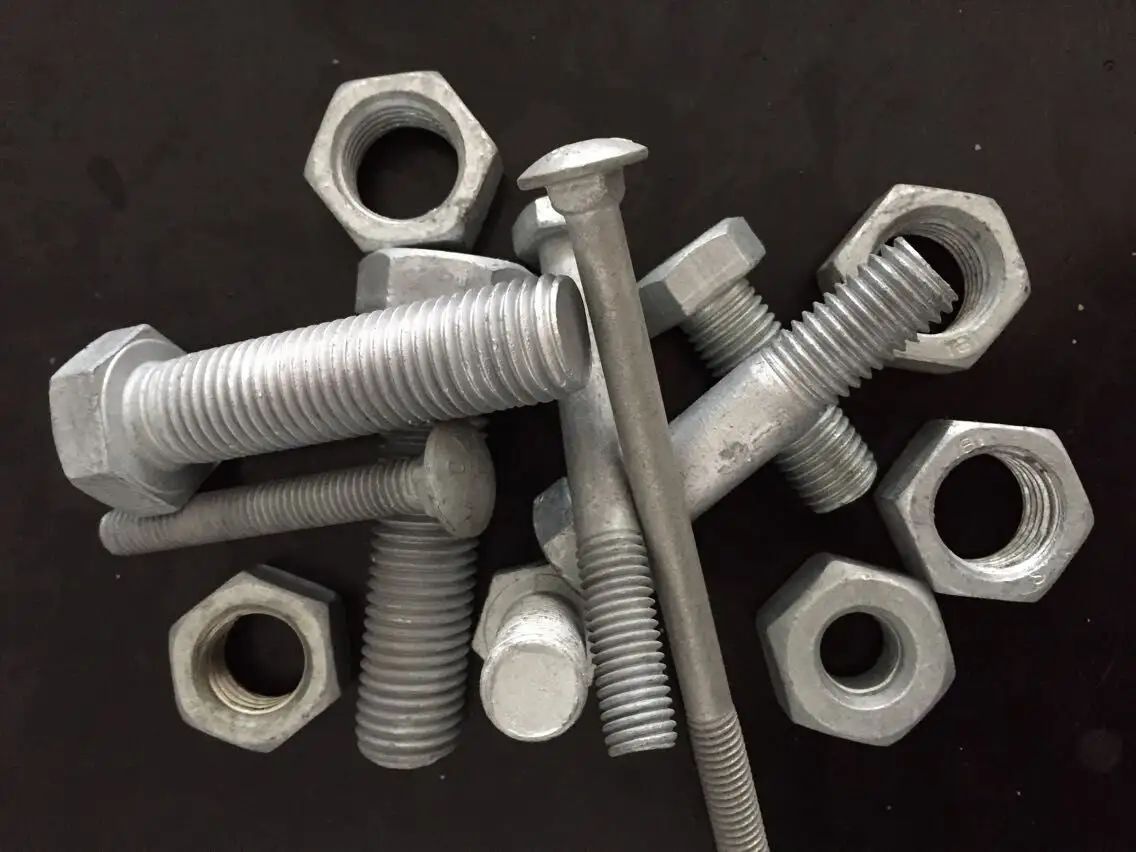
8. Infiltrácia zinku
Infiltrácia zinku je pevná metalurgická tepelná difúzna povlaky zinočnatého prášku. Jeho uniformita je dobrá a v nite aj slepých otvoroch je možné získať rovnomernú vrstvu. Hrúbka pokovovania je 10-110 μm. A chybu je možné kontrolovať na 10%. Jeho pevnosť viazania a antikorózne výkony so substrátom sú najlepšie v zinkových povlakoch (ako je elektrogalvanizácia, hor s horúcim spisom a Dacromet). Jeho proces spracovania je bez znečistenia a najpriaznivejší.
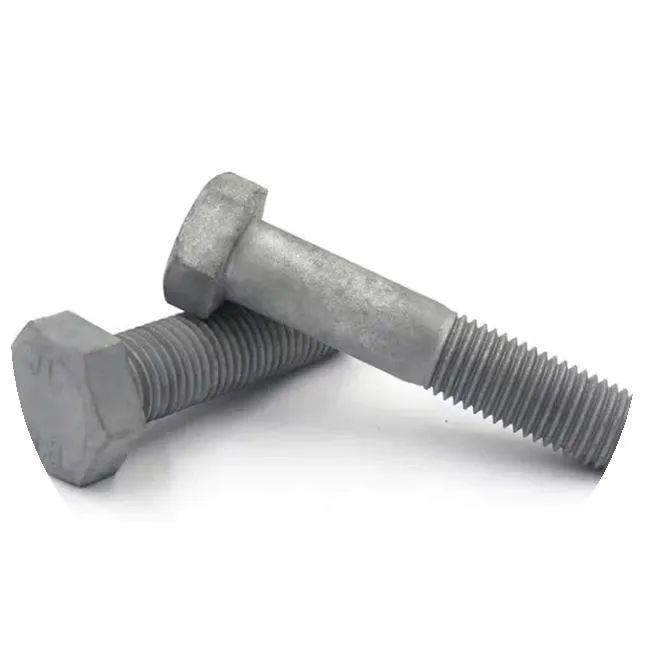
9. Dacromet
Neexistuje žiadny problém s vodíkovým stĺpcom a výkon konzistencie krútiaceho momentu je veľmi dobrý. Bez ohľadu na problémy s chrómom a životným prostredím je DACROMET v skutočnosti najvhodnejšími pre upevňovacie prvky s vysokou pevnosťou s vysokými požiadavkami na protikoróziu.
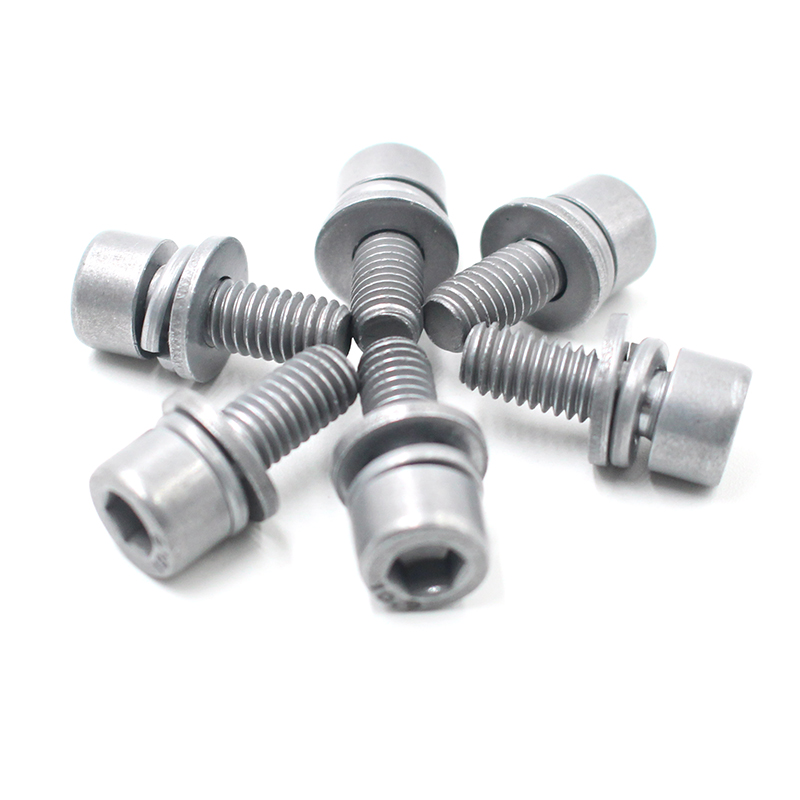
Čas príspevku: máj 19-2023