Výber povrchovej úpravy je problém, s ktorým sa stretáva každý dizajnér.K dispozícii je veľa druhov povrchových úprav a dizajnér na vysokej úrovni by mal zvážiť nielen hospodárnosť a praktickosť dizajnu, ale venovať pozornosť aj procesu montáže a dokonca aj ekologickým požiadavkám.Nižšie je uvedený krátky úvod k niektorým bežne používaným povlakom spojovacích materiálov založených na vyššie uvedených princípoch, aby ich mohli použiť odborníci v oblasti spojovacích materiálov.
1. Elektrogalvanizácia
Zinok je najbežnejšie používaný povlak pre komerčné spojovacie prvky.Cena je relatívne nízka a vzhľad je dobrý.Medzi bežné farby patrí čierna a vojenská zelená.Jeho antikorózny výkon je však priemerný a jeho antikorózny výkon je najnižší spomedzi vrstiev zinkovania (povlaku).Vo všeobecnosti sa neutrálny test soľným postrekom galvanizovanej ocele vykonáva do 72 hodín a používajú sa aj špeciálne tesniace prostriedky, aby sa zabezpečilo, že test neutrálnym soľným postrekom bude trvať viac ako 200 hodín.Cena je však drahá, čo je 5-8 násobok bežnej pozinkovanej ocele.
Proces elektrogalvanizácie je náchylný na vodíkové krehnutie, takže skrutky nad stupňom 10,9 nie sú vo všeobecnosti ošetrené galvanizáciou.Aj keď je možné vodík odstrániť pomocou pece po pokovovaní, pasivačný film sa poškodí pri teplotách nad 60 °C, takže odstránenie vodíka sa musí vykonať po galvanickom pokovovaní a pred pasiváciou.To má zlú prevádzkyschopnosť a vysoké náklady na spracovanie.V skutočnosti všeobecné výrobné závody aktívne neodstraňujú vodík, pokiaľ to nepožadujú konkrétni zákazníci.
Konzistencia medzi krútiacim momentom a silou predbežného utiahnutia pozinkovaných spojovacích prvkov je zlá a nestabilná a vo všeobecnosti sa nepoužívajú na spájanie dôležitých častí.Aby sa zlepšila konzistencia predpätia krútiaceho momentu, metóda nanášania mazacích látok po pokovovaní sa môže použiť aj na zlepšenie a zlepšenie konzistencie predpätia krútiaceho momentu.
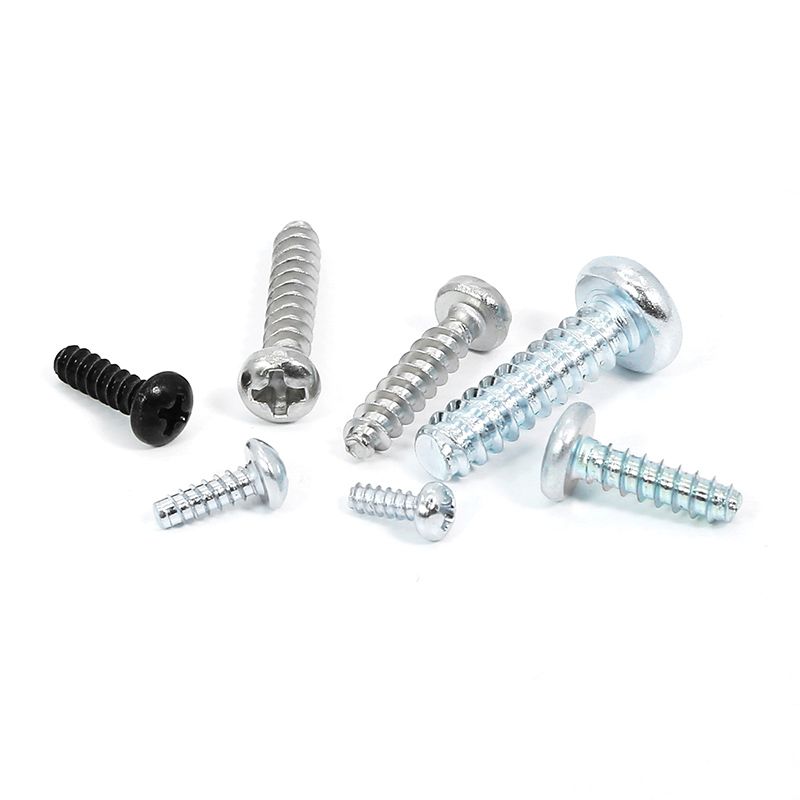
2. Fosfátovanie
Základným princípom je, že fosfátovanie je relatívne lacnejšie ako galvanizácia, ale jeho odolnosť proti korózii je horšia ako galvanizácia.Po fosfátovaní by sa mal aplikovať olej a jeho odolnosť proti korózii úzko súvisí s výkonnosťou aplikovaného oleja.Napríklad po fosfátovaní, nanesení všeobecného antikorózneho oleja a vykonaní testu neutrálnym soľným postrekom iba na 10-20 hodín.Aplikácia vysokokvalitného oleja proti hrdzi môže trvať až 72-96 hodín.Jeho cena je však 2-3 krát vyššia ako cena bežného fosfátovacieho oleja.
Existujú dva bežne používané typy fosfátovania pre upevňovacie prvky, fosfátovanie na báze zinku a fosfátovanie na báze mangánu.Fosfátovanie na báze zinku má lepší mazací výkon ako fosfátovanie na báze mangánu a fosfátovanie na báze mangánu má lepšiu odolnosť proti korózii a opotrebeniu ako zinkovanie.Môže sa používať pri teplotách v rozmedzí od 225 do 400 stupňov Fahrenheita (107-204 ℃).Najmä na pripojenie niektorých dôležitých komponentov.Ako sú skrutky a matice ojnice motora, hlavy valcov, hlavného ložiska, skrutky zotrvačníka, skrutky a matice kolies atď.
Skrutky s vysokou pevnosťou používajú fosfátovanie, čo môže tiež zabrániť problémom s vodíkovým skrehnutím.Preto skrutky nad stupňom 10,9 v priemyselnej oblasti zvyčajne používajú fosfátovú povrchovú úpravu.
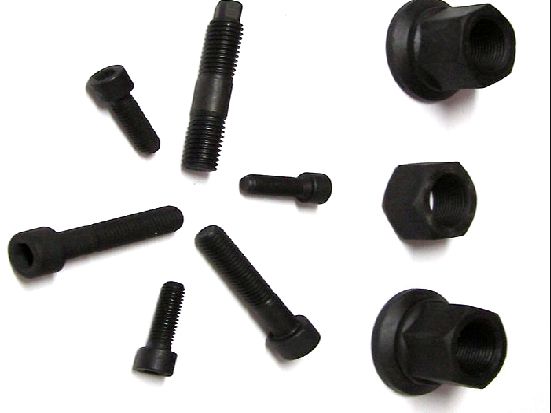
3. Oxidácia (sčernenie)
Černenie+olejovanie je obľúbený náter na priemyselné spojovacie prvky, pretože je najlacnejší a vyzerá dobre pred spotrebou paliva.Vďaka svojmu sčerneniu nemá takmer žiadnu antikoróznu schopnosť, takže bez oleja rýchlo zhrdzavie.Aj v prítomnosti oleja môže test soľným postrekom trvať len 3-5 hodín.
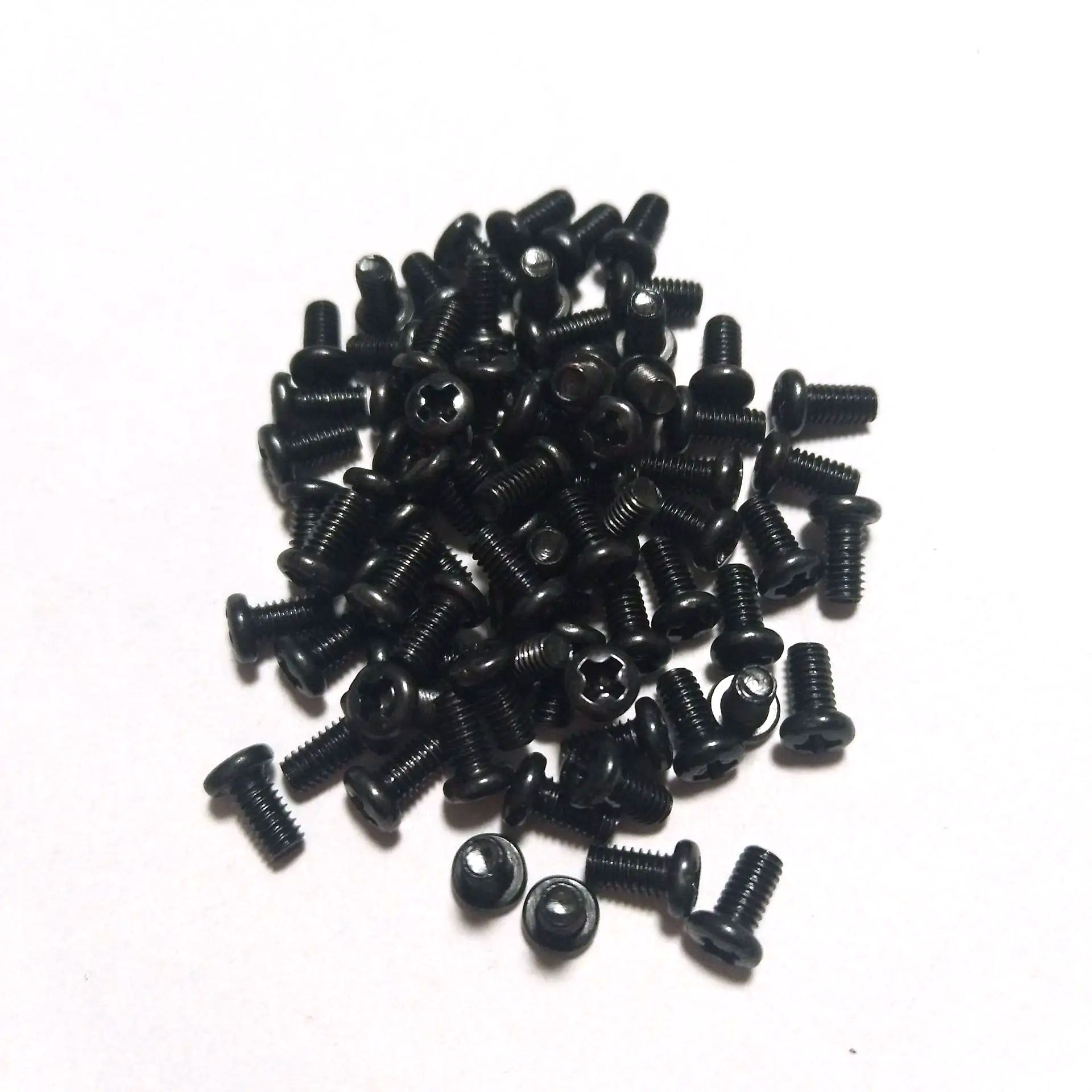
4. Galvanizačná priečka
Kadmium má vynikajúcu odolnosť proti korózii, najmä v morskom atmosférickom prostredí, v porovnaní s inými povrchovými úpravami.Náklady na spracovanie odpadovej kvapaliny v procese galvanického pokovovania kadmiom sú vysoké a jeho cena je asi 15-20 krát vyššia ako pri galvanickom pokovovaní zinku.Nepoužíva sa teda vo všeobecných odvetviach, len pre špecifické prostredia.Upevňovacie prvky používané pre plošiny na ťažbu ropy a lietadlá HNA.
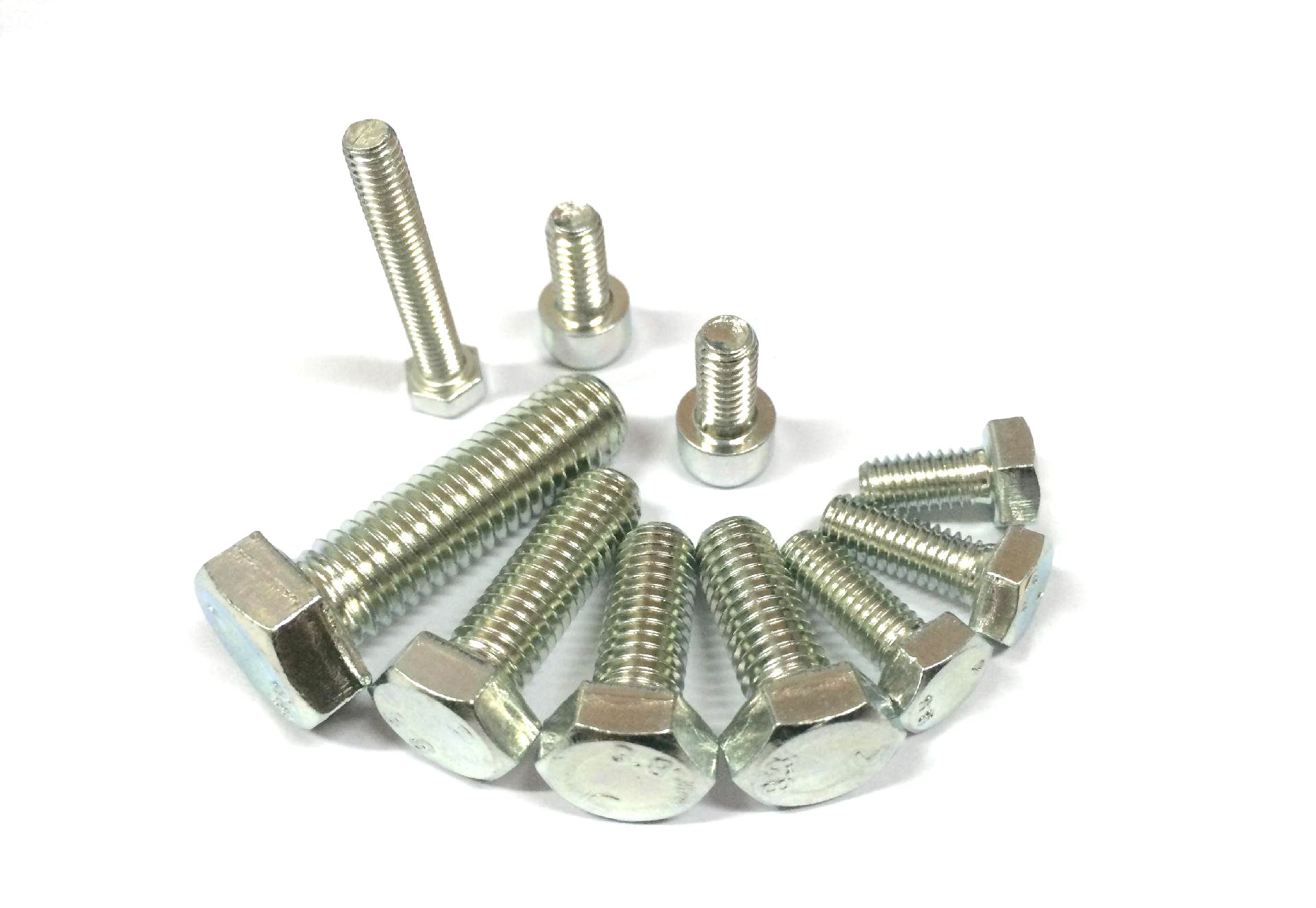
5. Chrómovanie
Chrómový povlak je veľmi stabilný v atmosfére, nie je ľahké zmeniť farbu a stratiť lesk a má vysokú tvrdosť a dobrú odolnosť proti opotrebovaniu.Použitie chrómovania na spojovacích prvkoch sa všeobecne používa na dekoratívne účely.Zriedkavo sa používa v priemyselných oblastiach s vysokými požiadavkami na odolnosť proti korózii, pretože dobré pochrómované spojovacie prvky sú rovnako drahé ako nehrdzavejúca oceľ.Iba ak je pevnosť nehrdzavejúcej ocele nedostatočná, namiesto toho sa používajú chrómované spojovacie prvky.
Aby sa predišlo korózii, meď a nikel by sa mali pred chrómovaním najskôr pokovovať.Chrómový povlak vydrží vysoké teploty 1200 stupňov Fahrenheita (650 ℃).Ale je tu aj problém vodíkového krehnutia, podobne ako pri galvanizácii.
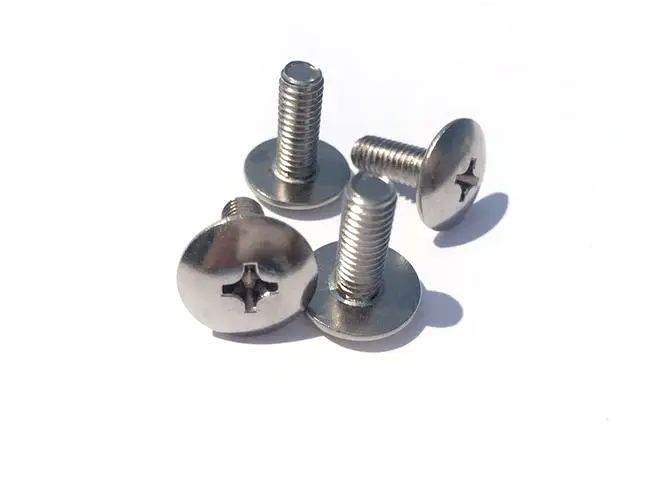
6. Poniklovanie
Používa sa hlavne v oblastiach, ktoré vyžadujú antikoróznu ochranu a dobrú vodivosť.Napríklad výstupné svorky batérií vozidiel.
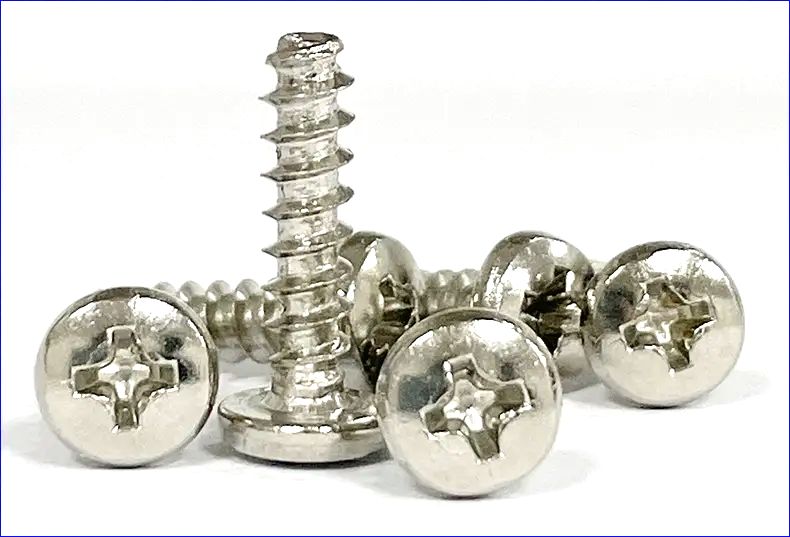
7. Žiarové zinkovanie
Žiarové zinkovanie je tepelný difúzny povlak zinku zahriaty na kvapalinu.Hrúbka povlaku je medzi 15 a 100 μm.A nie je ľahké ho ovládať, ale má dobrú odolnosť proti korózii a často sa používa v strojárstve.Počas procesu žiarového zinkovania dochádza k silnému znečisteniu vrátane zinkového odpadu a zinkových pár.
Kvôli hrubému povlaku spôsobil ťažkosti pri zaskrutkovaní vnútorných a vonkajších závitov spojovacích prvkov.Kvôli teplote spracovania žiarovým zinkovaním sa nemôže použiť pre spojovacie prvky nad 10,9 (340 ~ 500 ℃).
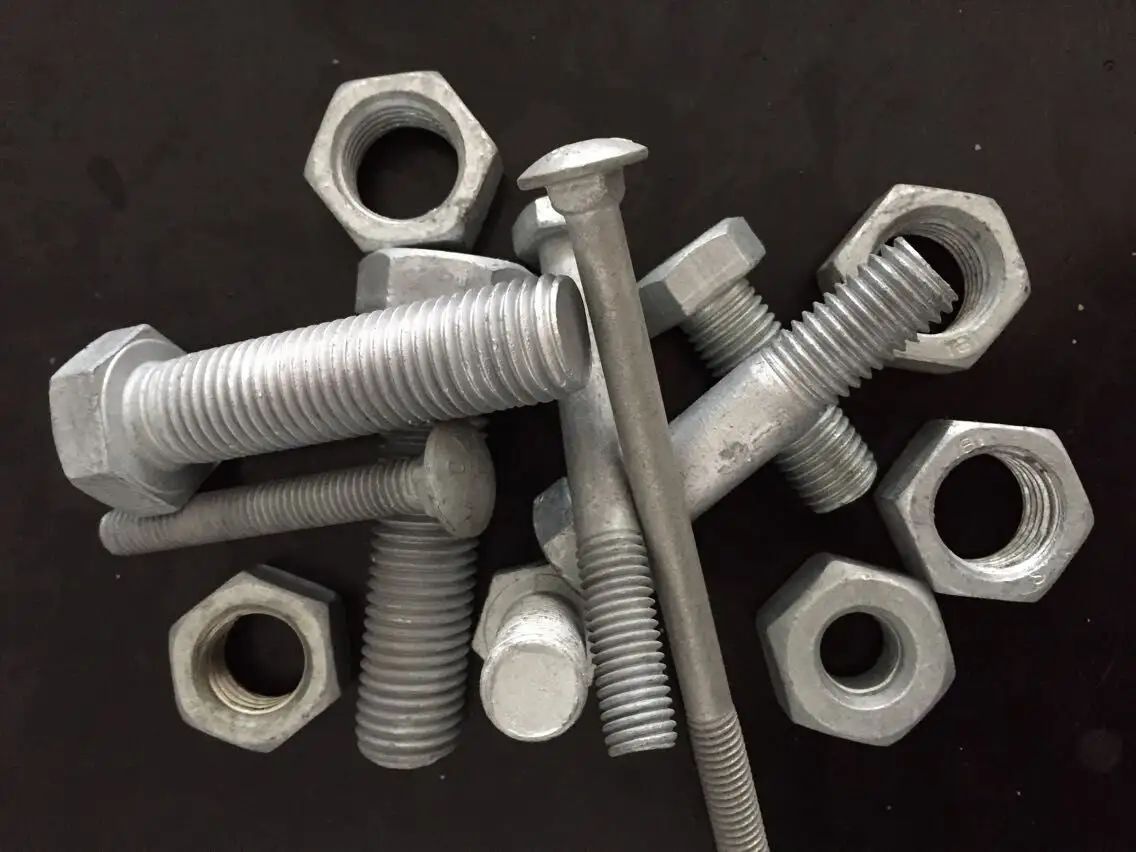
8. Infiltrácia zinku
Zinková infiltrácia je pevný metalurgický tepelne difúzny povlak zinkového prášku.Jeho rovnomernosť je dobrá a možno dosiahnuť rovnomernú vrstvu v závitoch aj slepých otvoroch.Hrúbka pokovovania je 10-110 μm.A chyba môže byť kontrolovaná na 10%.Jeho priľnavosť a antikorózne vlastnosti s podkladom sú najlepšie pri zinkových povlakoch (ako je elektrogalvanizácia, žiarové zinkovanie a Dacromet).Proces jeho spracovania je bez znečistenia a najekologickejší.
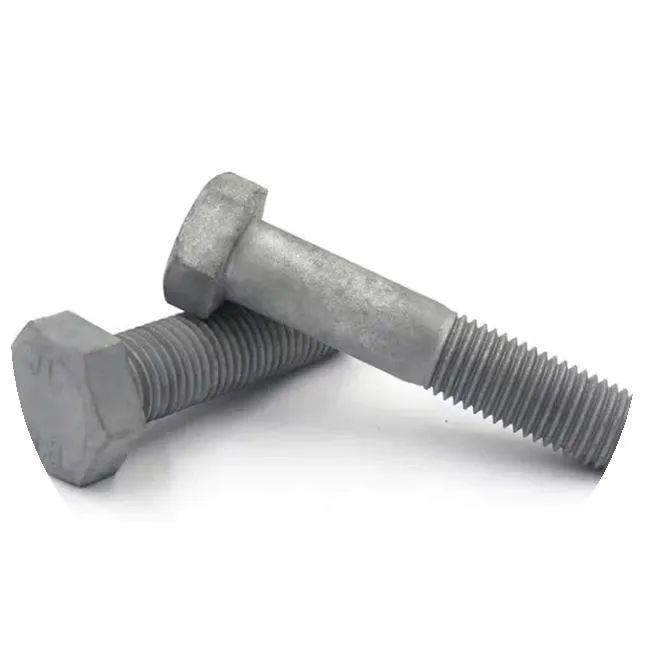
9. Dacromet
Neexistuje žiadny problém s vodíkovým skrehnutím a výkon konzistentnosti predpätia krútiaceho momentu je veľmi dobrý.Bez ohľadu na otázky chrómu a životného prostredia je Dacromet v skutočnosti najvhodnejší pre vysokopevnostné spojovacie prvky s vysokými požiadavkami na antikoróznu ochranu.
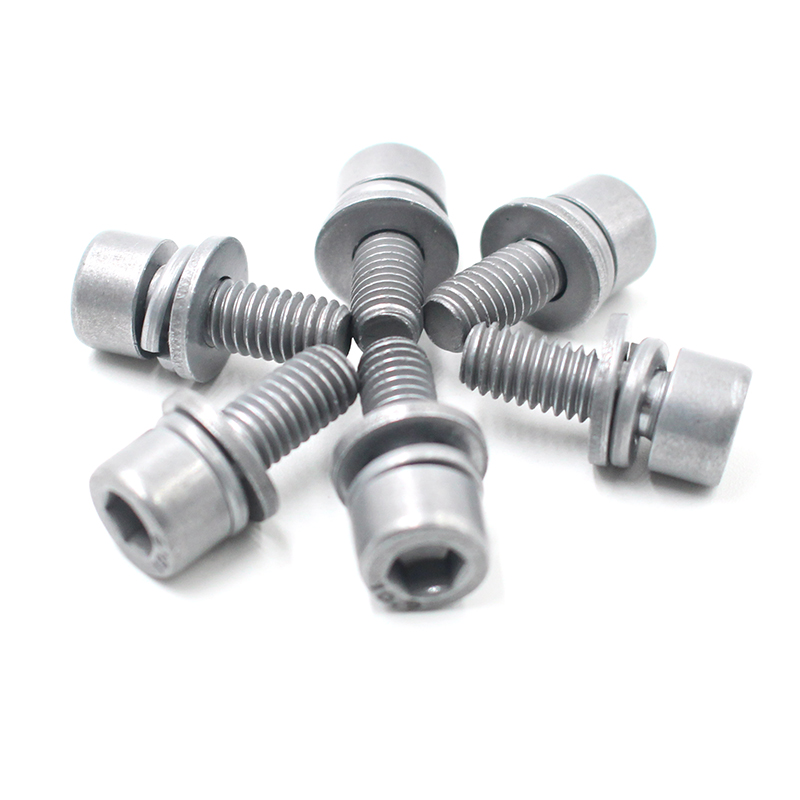
Čas odoslania: 19. mája 2023